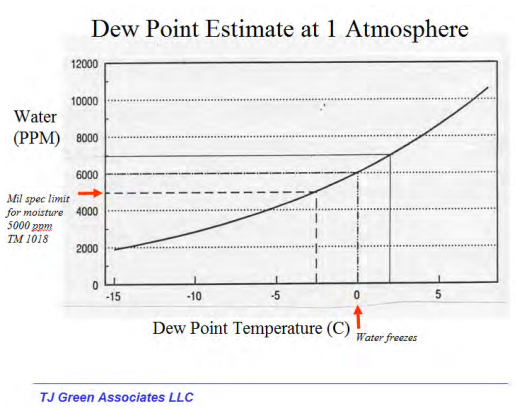
Hermetic vs “Near Hermetic” Packaging A Technical Review
September 21, 2016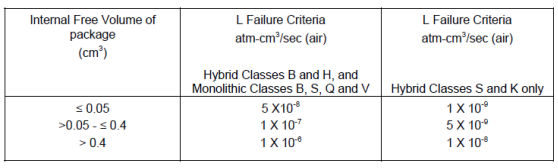
TM 1014 Update and Hermeticity Spec Change
September 28, 2016Non-Hermetic Packaging For Military And Aerospace
Hermetic packaging of components for military and aerospace applications is a proven baseline with a successful forty year track record. Recently, packages made from polymers such as liquid crystal polymer LCP, or with robust moisture barrier coatings, have been introduced into the marketplace and hold the promise of reliable operation at a greatly reduced cost and weight. In some cases, new devices types are only available in non-hermetic packages.
What the heck is “Non-hermetic”? or “Near”? or “Quasi”?
By definition hermetic packages are made from glasses, metals or ceramics whereby the moisture permeability through the bulk material is negligible. Hermetic packages pass the testing described in MIL-STD-883 TM 1014, the universal standard for hermeticity. “Non-hermetic” is anything that is not hermetic including anything made with polymeric materials including LCP. Molded plastic parts on lead frames for SMT processing, including plastic BGA’s are all non-hermetic. “Near hermetic” packaging was a term used by Ken Gilleo about ten years ago.
It was an attempt to describe engineered plastic packages with materials and processes (thermoplastics and specialized coatings) that are good enough to meet the customer performance requirements and expected lifetimes in the end use environment. The term “Quasi-hermetic” is just an off shoot of “near-hermetic”. Both terms have been used by package suppliers to differentiate their packages from conventional plastic or PEMS type packages and gain acceptance within the community.
Fig 1: Non-hermetic telecom power package
Hermeticity and the need for change, divergent views
Ironically, within the aerospace community there is a drive to tighten the hermeticity specifications and at the same time there is growing pressure by OEMs to explore alternative non-hermetic packaging technology as a way to cut cost. This is especially true in the hybrid microwave community where all gold metalized MMICs assembled using gold wire are somewhat less susceptible to moisture related failure mechanisms.
Fifteen years ago the auto industry moved away from hermetic packaging and instead mounted their corrosion prone power MOSFETS and IGBTs directly to heat sinks in plastic packages filled with special silicones, and then bolted these parts directly to an engine block. This is an extremely harsh environment, but the packaging approach has proven reliable.
Power packages used in the telecommunications industry, specifically those designed for base stations are now predominantly non -hermetic. A power transistor is soldered to a heat sink and an LCP lid is glued on top (See Fig. 1). There are many MEMS devices that work reliably in non-hermetic packages.
All the latest packaging developments are driven from the commercial world. Many state-of-the art ICs are only available in non-hermetic packages, for example Xilinx’s latest FPGA is no longer available in a hermetic configuration. So like it or not the aerospace community must get on board and finds ways to accommodate or harden packages in such a way as to minimize damage, for those devices truly susceptible to moisture. Granted, none of the industries mentioned above have the requirement to operate from -55 C to 125 C for a 10 or 20 year mission life. But do the current hermeticity specs really guarantee a dry package for 10 to 20 years?
How To Qualify
The million dollar question is how to properly qualify a non-hermetic package. The existing qualification and screen testing flows are clearly defined in MIL-PRF – 38534/5 for hermetic packages. The author’s biggest concern is that component suppliers will subject their non-hermetic packages to this testing sequence and present them as having passed TM 1014, which may well be the case. However, TM 1014 was never intended for “non-hermetic” packages and it’s quite possible for a cavity style LCP package to pass TM 1014, but that doesn’t make it hermetic.
The aerospace community, led by NASA, is rapidly addressing this concern with the introduction of a new quality designator for “non-hermetic” monolithic part types for space applications. The new quality classification is called “Class Y”. The latest release of MIL -PRF-38535 Rev K, 12/21/12 draft, publically available on the DLA website is out for review, and a coordination meeting is scheduled for April 2013. The latest issue of the hybrid specification MIL- PRF- 38534 contains an appendix that addresses “non-hermetic” cavity and non-cavity style packages.
Moisture Sensing inside a sealed cavity
One possibility to assess moisture uptake and egress in a non-hermetic package is to embed moisture sensors inside the cavity and measure real time how quickly and under what ambient conditions moisture accumulates inside. Below is a moisture sensor mounted inside a device which is then sealed with an epoxy and LCP lid. The sensors then accurately records and measures the humidity inside as a function of a changing ambient. Knowing this and given that most spacecraft are warmed up for several weeks prior to power on may enable the use of non-hermetic cavity devices provided the moisture egress is well characterized and doesn’t interfere with any optics. Internal gas analysis according to TM 1018 is also an appropriate test to provide a one-time snapshot of moisture condition, as well as the presence of other volatiles of concern, inside non-hermetic cavity packages.
Fig 2: Moisture Sensors
Concluding Thoughts
The use of non-hermetic packaging technology for military and aerospace applications holds the promise of lower cost and lighter weight packages. However, any perceived cost advantage at the component level must be weighed against the catastrophic cost of a system failure. The qualification and screening protocols are in the early development stage. Proceed with caution! Share your ideas and concerns on this important topic with your industry colleagues.