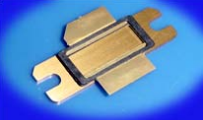
Non-Hermetic Packaging For Military And Aerospace
September 22, 2016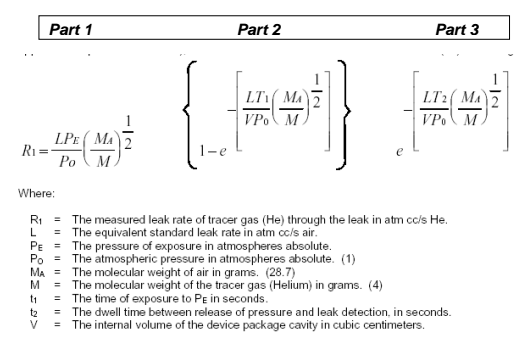
A Practical Guide to TM 1014 (Seal)
September 29, 2016TM 1014 Update and Hermeticity Spec Change
Mil-STD-883J was released on June 7th 2013 and within that document there was a significant change to the hermeticity test method 1014.14 (Seal). The hermeticity spec limit for space qualified hybrids was tightened by two orders of magnitude. The hermeticity specification for non-space products remained unchanged. TM 1014 is the defacto leak test hermeticity standard and is used and referenced by many companies in the defense, aerospace, telecom, RF and microwave, oil and gas and Class III medical device industries.
JEDEC along with DLA, Air Force and the rest of the community is presently reviewing another draft of TM 1014, which may add another leak test technique (condition A5) and clarify existing hermeticity test methodologies.
New TM 1014 Hermeticity Spec:
This spec change is significant and may require companies to purchase new hermeticity test equipment and may significantly reduce process yields for some part types and therefore impact cost and schedule. There is likely to be some issues and consternation adopting to the new spec limit.
Defense Land and Maritime has allocated a two year implementation window which is closing fast, the deadline is June of 2015. For the time being this spec change only affects Space qualified Class K hybrids, however, once the test equipment is in place it may well be that down the road the tighter leak spec requirement are levied on all hermetically sealed microcircuits. It’s already a requirement for small volume semiconductor devices built to MIL-PRF-19500 performance specification.
Moisture is a bad. Any amount of moisture beyond the 5000 PPM specification level increases the probability that moisture may condense on a surface as the temperature drops and thereby be present in liquid form to assist in a moisture related failure mechanism. The deleterious effect of moisture on reliability of microelectronics has been well chronicled over the years. The TM 1014 spec has always been very lenient in many respects. A package leaking at or near Lair =1E-06 cc/sec is going to exchange its atmosphere in a matter of months not years. This is well known and has been the case for many years. However, I haven’t seen any compelling statistical evidence that suggests a tighter leak spec will improve reliability or eliminate moisture related failures.
Most conventional helium mass spectrometry (HMS) leak detectors lack the precision and sensitivity to measure leak rates to the new spec. However, it is possible to achieve the desired sensitivity if one is willing to “helium bomb” the parts for some ridiculous amount of time like 100 hours or so. A two order magnitude reduction in the Lair spec limit from 1E-06 cc/sec to 1E-08 cc/sec requires equivalent HMS readings to be in the low 1E-10 or 1E-11 cc/sec helium range, for typical bomb time and pressure conditions. Large volume hybrids may require 100 hrs of more of helium bomb time. The noise floor for most conventional HMS equipment in existence today is about 3E-09 cc/se He in a production environment. Download the Howl and Mann leak rate calculator to determine the expected bomb time/pressure for your particular package type.
The blowback of the new spec change for most companies is the need to now purchase and qualify new leak testing equipment. That will be costly and time consuming. We are at a time in the industry where many are questioning the need for hermeticity and there are tremendous pressures from OEMs to reduce cost. It’s not likely that package suppliers will develop new hermetic feedthrough technologies, and what if the existing hermetic packages are incapable of meeting the tighter requirement and force expensive package redesigns.
There are basically three options for any company contemplating new equipment with a fourth option potentially on the horizon. The new release of TM 1014 describes in detail three techniques and procedures that are capable, and there is measured test data available to demonstrate compliance to the new tightened requirement. They are: Optical Leak Test (OLT), Cumulative Helium Leak Detection (CHLD) and Radioisotope Kr-85.
The test conditions for each of these test methods are totally different. The KR-85 radioisotope method forces a radioactive tracer gas Kr-85/Air mixture into a package and then counts the number of radioactive molecules that remain inside at ambient temperature and pressure conditions. CHLD extends the sensitivity of conventional HMS. Like HMS, CHLD detects a tracer gas, usually helium but not necessarily, forced into or sealed into the package and then measures a leak rate, or immediately identifies a gross leak by detecting a signal burst. In either case the escaping tracer gas is measured while the part is under vacuum. OLT on the other hand, precisely measures the lid or package deflection while the part is under pressure, and there is no injection of a tracer gas. OLT thus eliminates the concern of residual tracer gas on the surface, which tends to confound the results for both helium and Kr-85 testing. OLT also performs a gross and fine leak test in the same pass and is “fail safe” for gross leakers.
If the new version of TM 1014 causes you to have to purchase new equipment then my advice would be to evaluate all three methods and pick the one that best suits the leak rate requirement for your particular package type, package volume, expected throughput ect. Be especially careful that any new equipment is able to detect and fail for any possible “gross leakers”. Gross leaks are a major cause for concern because they can easily lead to early field failures. In my opinion there isn’t a big difference in a part leaking at 2E-09 Lair vs. 9E-10 Lair, but there surely is a problem in “gross leak” escapes that evade detection and get built up into our military systems.
Remember in any correlation study to convert everything back to “air equivalent” leak rates for data used for comparison purposes. This can be tricky and keep in mind for the reasons stated above precise “correlation” amongst the three methods may not be achievable. However, based on my experience all three methods are capable of meeting the new specs and are scientifically sound. They also agree reasonable well with each other when viewed as “go/no-go” attributes data. That is what hermeticity testing is all about, a one time check on the seal process done on the factory floor under idealized conditions. To use the leak test data to make reliability predictions or project expected lifetimes in the field is fraught with problems. The first of which is relating the measured leak rate to an actual theoretical model to predict moisture ingress into a sealed enclosure, then factor in the moisture susceptibility of the components inside….not for the lighthearted.
Each one of these major methods has advantages and disadvantages so buyer beware!