Moisture in Microelectronics: Physics and Chemistry of Volatile Species in Hermetic Electronic Devices
March 12, 2018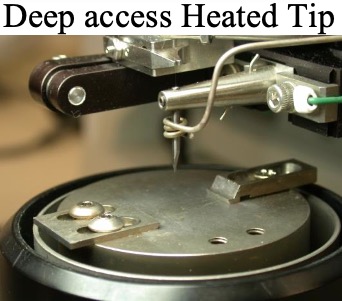
Wirebond Challenges in Microwave RF MMIC Modules for Military and Space
May 18, 2022Silver Epoxy Turns Black After an Oxygen Plasma Clean Prior to Wire Bonding…But So What?
Thomas Green
TJ Green Associates, LLC
739 Redfern Lane,
Bethlehem, PA 18017
email: [email protected]
Philipp wh Schuessler
Schuessler Consulting
[email protected]
ABSTRACT
In the early 1970s component manufacturers switched to epoxies for die attach in lieu of a eutectic attach. Resin bleed out was a common problem with these early epoxies and still is today. Resin bleed is difficult to see unless a filtered light source is connected to the microscope. The easiest and most effective manner to clean epoxy resin bleed, and other outgassed organic species, is to expose the assembly to a UV Ozone or an O2 plasma treatment just prior to wire bonding. However, oxygen plasma turns the silver die attach epoxy black. Customers often take offense to this color change and hence O2 plasma cleaning prior to wirebond in large microwave hybrids and for other product types is normally not performed. Argon plasma is used instead.
This presentation reviews the chemistry involved in the formation of “black epoxy” and how the silvery epoxy appearance can easily be restored, thereby allowing for a more aggressive clean prior to wirebond. Rework of wire no sticks or multiple wirebond attempts on the same pad is a major concern in the manufacture of large area Hybrids and RF MMIC microwave hybrids and a big contributor to expensive rework cycles. How to effectively clean up resin bleed and deal with the “black epoxy” is the subject of this white paper
Key Words: Oxygen plasma clean,UV Ozone, Resin bleed, black silver epoxy, Visual Inspection, MIL-STD-883 TM 2017 , Blue Light inspection methods
Rework is a major problem faced by all in this industry:
The manufacture and assembly of hermetic high reliability Hybrids, RF microwave modules, 5G technology and Class III medical implants is a very challenging undertaking involving many process steps, a myriad of materials and mile long BOMs. Epoxy dispense, component placement, wirebond and hermetic seal are the critical processes that all need to be optimized as each flow into the other and in the end determine product reliability and company profitability. Rework is every company’s Achilles’ heel. This “hidden factor” as they used to call it, is a substantial part of most cost overruns, schedule delays and diminished quality.
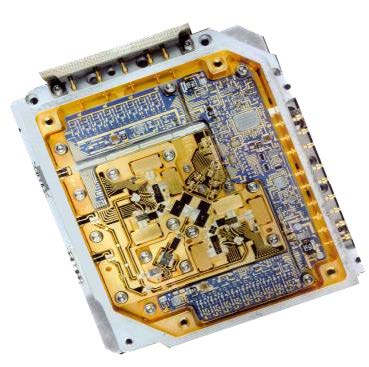
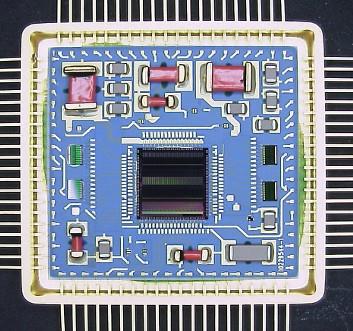
Removal and replacement of ICs and MMICs (Monolithic Microwave Integrated Circuits) is especially problematic. This rework step involves locally heating of the component above the epoxy Glass Transition Temperature (Tg) of the epoxy underneath, getting a flat screwdriver or tool under the die and digging it out. This inevitably creates collateral damage in terms of loose FM/F.O.D (Foreign Material/Foreign Object Debris) as the die can shatter and cause unintended collateral damage to nearby components. These loose conductive particles are a major reliability concern in any cavity sealed device and is addressed in detail in all the MIL- STD-883 visual inspection test methods. The dried silver epoxy then has to be scraped clean and new wet epoxy dispensed. A new component has to be carefully placed and sent to the cure oven for a second time. Next comes…
CLICK HERE TO DOWNLOAD THE FULL 12 PAGE TECHNICAL WHITE PAPER